集装箱装柜软件智能算法优化三维可视化装柜方案指导技术文档
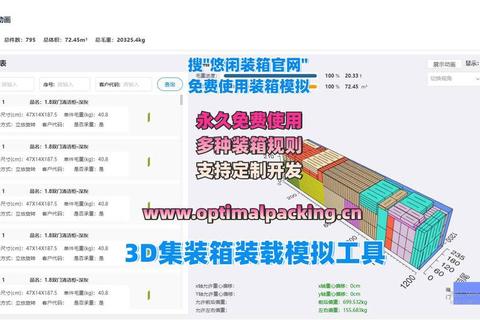
1. 应用场景与核心价值
集装箱装柜软件智能算法优化三维可视化装柜方案指导(以下简称“智能装柜系统”)是一款面向物流、制造、贸易等多行业的数字化工具,旨在通过智能算法与三维可视化技术解决传统装柜效率低、空间浪费大、操作风险高等问题。其核心价值包括:
提升装载率:通过优化算法自动生成货物摆放方案,平均提升集装箱空间利用率5%-15%。
降低人工成本:替代传统CAD手工规划,减少80%以上人力投入。
保障运输安全:实时计算货物重心,避免因装载不平衡导致的运输事故,尤其适用于危化品、重型设备等特殊场景。
全流程数字化:支持装箱指导图、3D动画、报关单生成等功能,实现从规划到执行的链路闭环。
典型应用场景包括:
海运拼柜:针对跨国零售、新能源行业的多品类混装需求,生成标准化拼柜方案。
循环取送(Milkrun):优化路径与装载顺序,降低运输成本。
危化品运输:自动识别货物堆码规则,规避安全风险。
2. 智能算法优化技术解析
智能装柜系统的核心能力依赖于以下算法架构与优化技术:
2.1 多维装箱算法
三维空间优化算法:基于强化学习的动态规划算法,支持不规则货物混装,自动计算货物朝向与摆放位置,最大化集装箱容积利用率。
遗传算法与启发式规则结合:通过迭代优化生成近似最优解,适应大规模复杂场景(如多托盘混装、多集装箱协同)。
实时重心计算:结合力学模型,确保货物堆叠稳定性,满足铁路、海运等场景的重心偏移限制。
2.2 规则配置与约束管理
系统支持自定义规则库,包括:
物理约束:货物承重限制、危化品隔离距离等。
业务约束:装柜优先级、客户指定摆放区域等。
合规约束:国际运输标准(如ISO 1496)及海关申报要求。
2.3 动态调整与协同优化
用户可通过3D界面手动调整方案,系统实时更新装载率与重心数据,支持多方案对比。
3. 三维可视化方案实施流程
集装箱装柜软件智能算法优化三维可视化装柜方案指导的核心操作流程分为以下步骤:
3.1 数据输入与预处理
货物信息:支持批量导入货物尺寸、重量、类别等属性,兼容Excel、ERP系统对接。
集装箱参数:内置标准集装箱型号(如20GP、40HQ),支持自定义尺寸。
3.2 算法计算与方案生成
一键算箱:5秒内生成初始方案,提供装载率、重心偏移量等关键指标。
多方案推荐:根据“装载率优先”“成本最优”等策略生成备选方案。
3.3 3D可视化交互与调整
动态渲染:支持360°旋转、分层查看货物堆叠细节,高亮显示危化品、易碎品等特殊货物。
碰撞检测:自动识别货物重叠区域,提供修正建议。
操作指引导出:生成装箱步骤图与动画,指导现场作业。
3.4 报告输出与系统对接
装箱报告:包含货物清单、装载率统计、重心位置等数据。
API集成:支持与WMS、TMS系统对接,实现装柜数据自动同步。
4. 系统配置与部署要求
4.1 软件版本与功能适配
| 版本 | 适用场景 | 核心功能 |
| 精简版 | 中小型企业基础估算 | 基础3D可视化、单次算箱 |
| 专业版 | 复杂业务规则与多集装箱协同 | 多方案对比、规则库管理、API对接 |
| 企业定制版 | 大型集团私有化部署 | 定制算法开发、全链路系统集成 |
4.2 硬件与网络要求
计算性能:专业版需4核CPU、16GB内存,支持GPU加速渲染。
存储空间:企业版建议预留500GB以上数据库容量。
网络环境:SaaS版本需稳定互联网连接,延迟≤100ms。
5. 典型应用案例分析
案例1:零售行业海运集拼
某跨国零售企业使用集装箱装柜软件智能算法优化三维可视化装柜方案指导,实现90%平均装载率,规划时间缩短至8分钟,人力成本降低90%。
案例2:新能源设备出口
通过算法优化12%的综合效率,完全替代人工CAD规划,生成符合国际标准的装箱方案,助力业务出海。
案例3:危化品多式联运
针对筒形与箱型货物混装需求,系统自动隔离不相容品类,生成合规报关图纸,提升订单履约效率100%。
6. 实施规范与安全合规
数据安全:通过ISO27001认证,支持私有化部署与数据加密。
行业合规:符合《集装箱标准体系(2023)》中安全智能集装箱技术要求。
运维支持:提供7×24小时技术响应,定期更新算法规则库。
集装箱装柜软件智能算法优化三维可视化装柜方案指导通过技术创新与场景适配,正在重塑全球物流行业的作业模式。未来,随着AI与物联网技术的深度融合,该系统将进一步向自动化、智能化方向演进,为供应链降本增效提供持续动力。